Why Lignin Extraction Usually Comes with a Catch
May 29, 2023 /
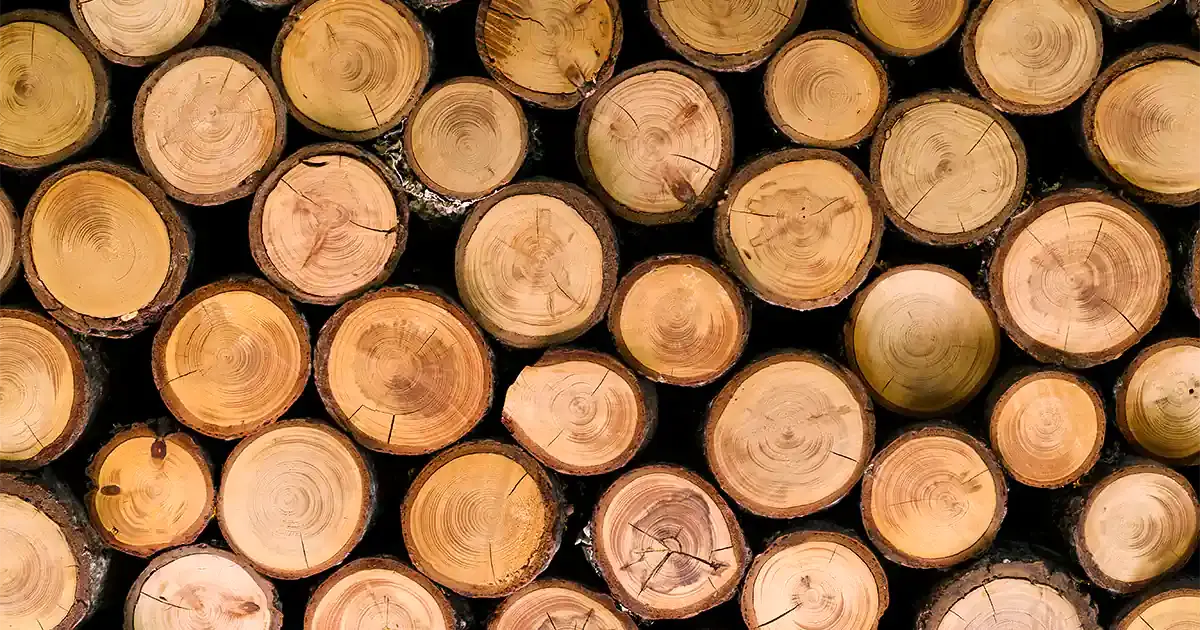
Many pulp and paper mills are looking for ways to compensate for the environmental impact of their operations while reaching global and internal sustainability goals. One common approach is enabling the possibility to replace oil as a building block in the production of high-value products with lignin. A natural fiber in almost every living plant, lignin plays a large role in wood’s ability to retain its characteristic stiffness and resiliency against decay.
Not only does lignin present amazing opportunities to replace fossil-based materials with renewable materials, but it can also decrease the discharge of pollutants. However, lignin extraction comes with a catch.
The high costs and safety risks of lignin extraction
Before lignin can be put to use as an alternative building block, it must first be extracted from a by-product of the Kraft pulping process called Black Liquor. In addition to lignin, Black Liquor consists of hemicellulose and inorganic compounds. Black Liquor is used to supply pulp for the production of paper and other products and is typically burned in a recovery boiler to generate energy for the Kraft pulp mill even though the boiler’s main function is to recycle chemicals.
However, whether a mill chooses to extract lignin through acid precipitation, enzymatic treatment, membrane filtration, solvent extraction, or steam stripping, it typically comes with consequences that outpace the initial investment of enabling the extraction process.
When lignin is removed from Black Liquor, the quality of the fuel decreases since the extraction can increase the concentration of inorganic compounds in Black Liquor such as sodium, chlorine, and sulphur. This opens the door for intense fouling since mills must load more fuel into the recovery boiler to compensate for the decrease in heat value. That decrease will, in turn, increase the mill’s costs for keeping the boiler clean with steam sootblowing. Heavy fouling and scaling can, to a point, even cause safety issues.
Curbing the downsides of lignin extraction with High Impact Sootblowing System (HISS™)
Considering the risks involved in lignin extraction, it has become important for pulp and paper mills to carefully weigh the potential downsides and upsides before initiating the process. Having to increase the boiler load in order to compensate for the loss in production is often enough to deter most mills from making the investment. But introducing HISS™ to the process offers a compelling remedy.
Although current users of HISS™ utilize the system for different reasons, it can additionally be used to reduce the mills’ steam sootblowing expenses by reducing the amount of steam used by 30-45%. This means that sootblowing can take place twice as often with the same amount of steam or a combination of the two. Due to the nature of HISS™, it also prolongs boiler availability by reducing the need for maintenance-related shutdowns. The lifetime of different components is also prolonged since the amount of condensate build-up from the steam is reduced.
Therefore, whenever a mill is considering making a biorefinery investment they should ensure that lignin extraction and HISS™ go hand-in-hand.
HISS™ – Sootblow more, with less steam.
The patented High Impact Sootblowing System (HISS™) disrupts the “how we have always done it” approach to energy-intensive steam sootblowing. By operating the existing steam sootblowing system in a smarter and less wasteful way, half the steam and half the time can be saved. This leads to increased boiler efficiency, availability, and lifetime without installing any new sootblowers or rebuilding the boiler.
Latest news & articles
Why Lignin Extraction Usually Comes with a Catch
May 29, 2023 /
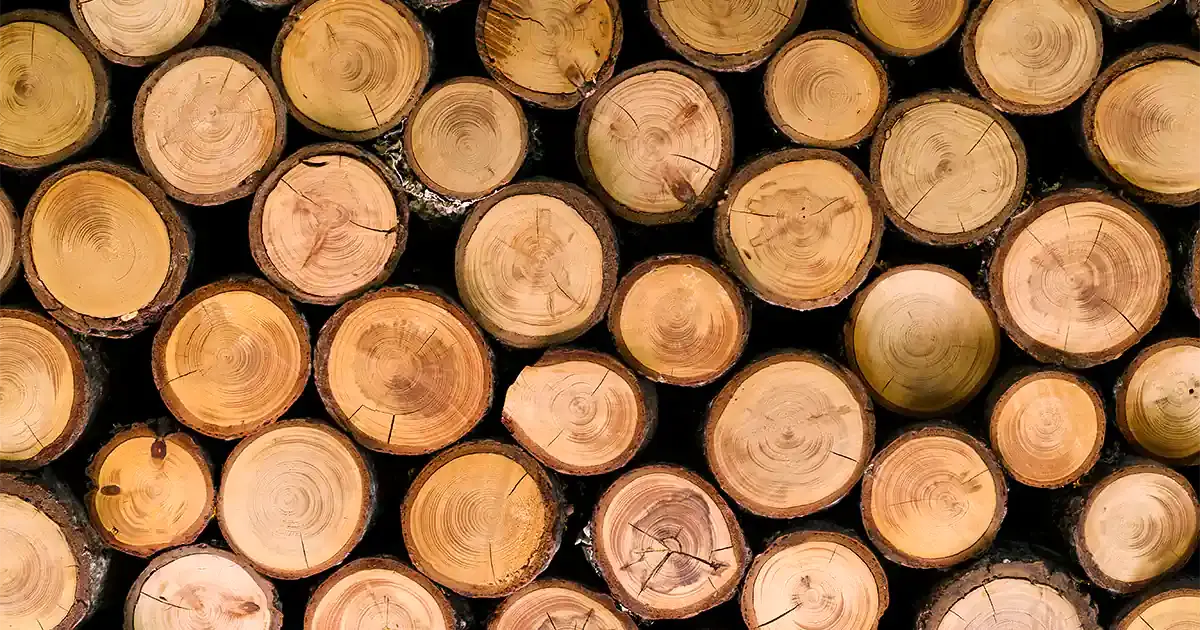
Many pulp and paper mills are looking for ways to compensate for the environmental impact of their operations while reaching global and internal sustainability goals. One common approach is enabling the possibility to replace oil as a building block in the production of high-value products with lignin. A natural fiber in almost every living plant, lignin plays a large role in wood’s ability to retain its characteristic stiffness and resiliency against decay.
Not only does lignin present amazing opportunities to replace fossil-based materials with renewable materials, but it can also decrease the discharge of pollutants. However, lignin extraction comes with a catch.
The high costs and safety risks of lignin extraction
Before lignin can be put to use as an alternative building block, it must first be extracted from a by-product of the Kraft pulping process called Black Liquor. In addition to lignin, Black Liquor consists of hemicellulose and inorganic compounds. Black Liquor is used to supply pulp for the production of paper and other products and is typically burned in a recovery boiler to generate energy for the Kraft pulp mill even though the boiler’s main function is to recycle chemicals.
However, whether a mill chooses to extract lignin through acid precipitation, enzymatic treatment, membrane filtration, solvent extraction, or steam stripping, it typically comes with consequences that outpace the initial investment of enabling the extraction process.
When lignin is removed from Black Liquor, the quality of the fuel decreases since the extraction can increase the concentration of inorganic compounds in Black Liquor such as sodium, chlorine, and sulphur. This opens the door for intense fouling since mills must load more fuel into the recovery boiler to compensate for the decrease in heat value. That decrease will, in turn, increase the mill’s costs for keeping the boiler clean with steam sootblowing. Heavy fouling and scaling can, to a point, even cause safety issues.
Curbing the downsides of lignin extraction with High Impact Sootblowing System (HISS™)
Considering the risks involved in lignin extraction, it has become important for pulp and paper mills to carefully weigh the potential downsides and upsides before initiating the process. Having to increase the boiler load in order to compensate for the loss in production is often enough to deter most mills from making the investment. But introducing HISS™ to the process offers a compelling remedy.
Although current users of HISS™ utilize the system for different reasons, it can additionally be used to reduce the mills’ steam sootblowing expenses by reducing the amount of steam used by 30-45%. This means that sootblowing can take place twice as often with the same amount of steam or a combination of the two. Due to the nature of HISS™, it also prolongs boiler availability by reducing the need for maintenance-related shutdowns. The lifetime of different components is also prolonged since the amount of condensate build-up from the steam is reduced.
Therefore, whenever a mill is considering making a biorefinery investment they should ensure that lignin extraction and HISS™ go hand-in-hand.
HISS™ – Sootblow more, with less steam.
The patented High Impact Sootblowing System (HISS™) disrupts the “how we have always done it” approach to energy-intensive steam sootblowing. By operating the existing steam sootblowing system in a smarter and less wasteful way, half the steam and half the time can be saved. This leads to increased boiler efficiency, availability, and lifetime without installing any new sootblowers or rebuilding the boiler.