Carbon capture project with cement producer Norcem will significantly lower carbon footprint using infrasound soot-cleaning
September 6, 2021 /
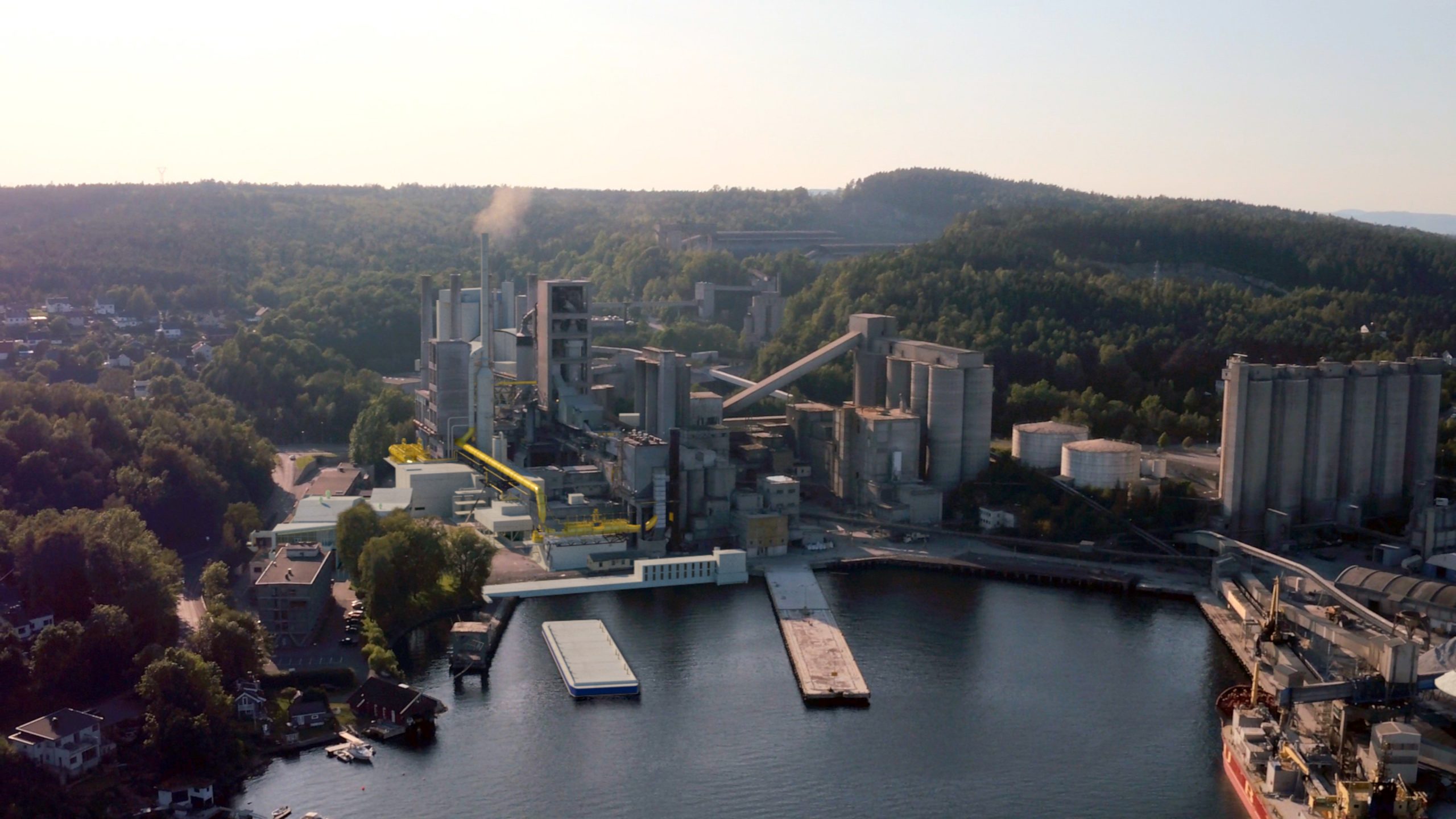
Image credited: Norcem Brevik Med CCS1
Cement is one of the most important commodities in the world. Norcem Brevik, owned by Heidelberg Cement, is the leading Norwegian cement supplier, aiming to become carbon neutral and reach national climate goals.
The Brevik Carbon Capture and Storage (CCS) project reduce CO2 emissions by 400,000 tonnes a year, paving the way for a net-zero carbon footprint for the cement lifecycle. Heat Management joins forces with Aker Carbon Capture by supplying powerful infrasound cleaning technology to keep the waste heat recovery boilers clean, thus maintaining a high heat transfer rate to maximize the boiler availability, efficiency, and lifetime.
Cement is the second most used commodity in the world after water, and the demand is increasing due to increased urbanization and population growth. Limestone is the key to make cement, breaking down limestone releases a significant amount of CO2, and there is currently no green option to match the characteristics of limestone. The Norwegian cement giant has taken innovative measures to tackle the problem from another angle, Carbon Capture and Storage. The Brevik CCS project is based on years of studies and testing, proving that CO2 capture is achievable.
The way it works is that flue gas is harnessed from the factory Chimney at Norcem Brevik. The flue gas is then cooled down by 30°C from 100-165°C in a direct contact cooler. The flue gas runs through an absorber, where the CO2 reacts with amine liquid, becoming an amine solution. Then the solution runs through a desorber, heating the liquid from 30°C to 120°C, separating the CO2, which can then be compressed and dried. This is an energy-intensive process that Norcem solves by utilizing waste heat from the cement factory. When the CO2 is returned to its liquid state, it is shipped by boat to a transit storage facility in Kollsnes. The result of the project is to avoid emitting 55 tons of CO2 per hour and 400 000 tons annually, which is equal to the emissions from about 200 000 cars per year.
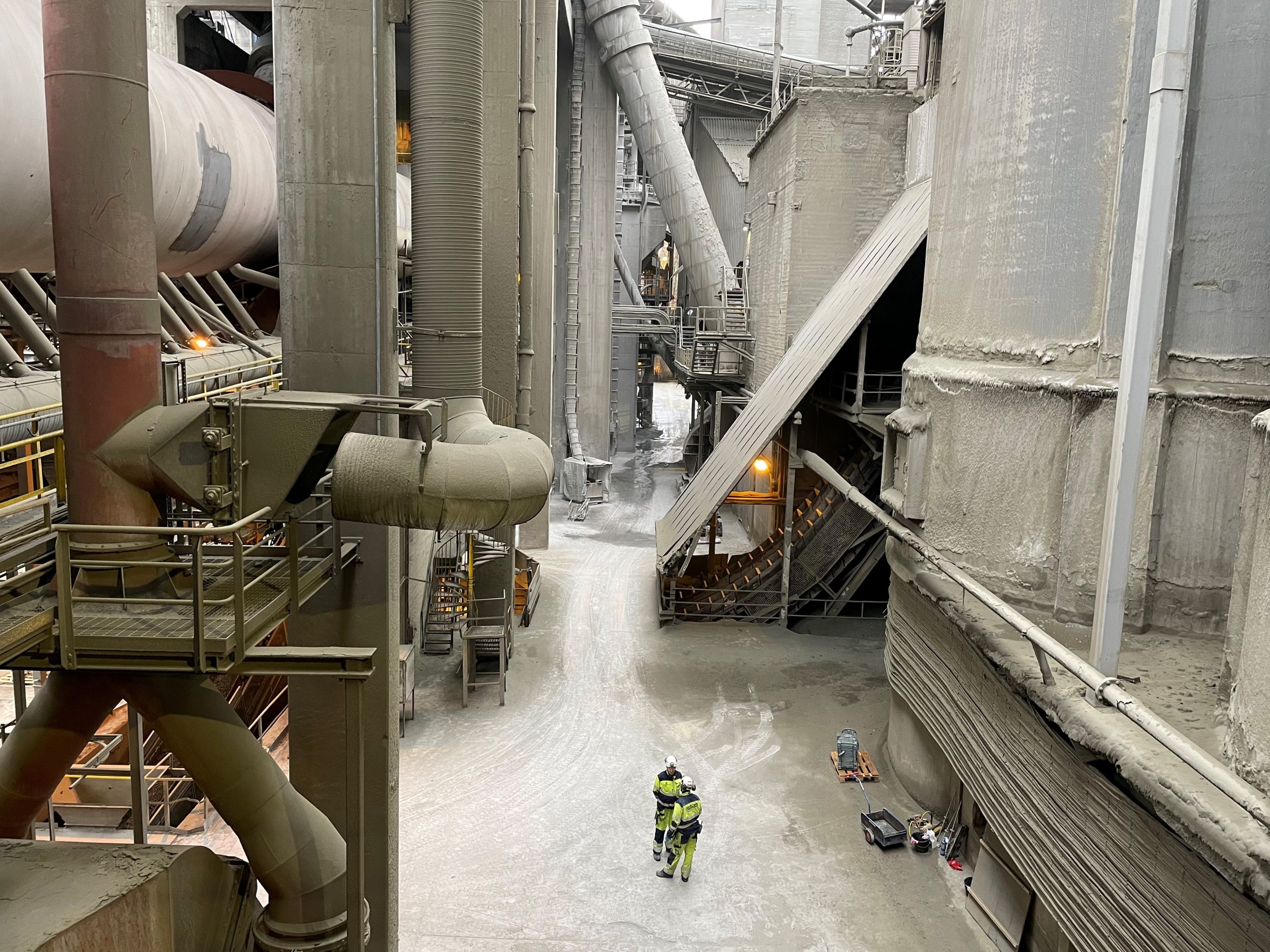
Image credited: Norcem Advansia
Cutting down on emissions and climate impact is a core value shared between Heidelberg Cement and Heat Management. Dirty boilers are a bottleneck for many companies. The cause of soot build-ups in boilers results in production losses, lower efficiency, unplanned stops for manual cleaning, among many other harmful effects. These issues cause unnecessarily high costs and environmental impact.
The Norcem project is a high dust application that often requires automatic, preventive, and dry online cleaning of all the heating surfaces. The unique Infrasound Cleaning system from Heat Management fit all the requirements and was successfully tested in a pilot plant before implementation in the full-scale plant. Heat Management ensures that the waste heat boilers run reliably and efficiently throughout the whole production year.
The sootcleaning system’s ability to help customers become more sustainable and save money simultaneously is what makes the system an incredible investment. More companies are encouraged to hop on the sustainability train, as sustainability is the new normal.
Latest news & articles
Carbon capture project with cement producer Norcem will significantly lower carbon footprint using infrasound soot-cleaning
September 6, 2021 /
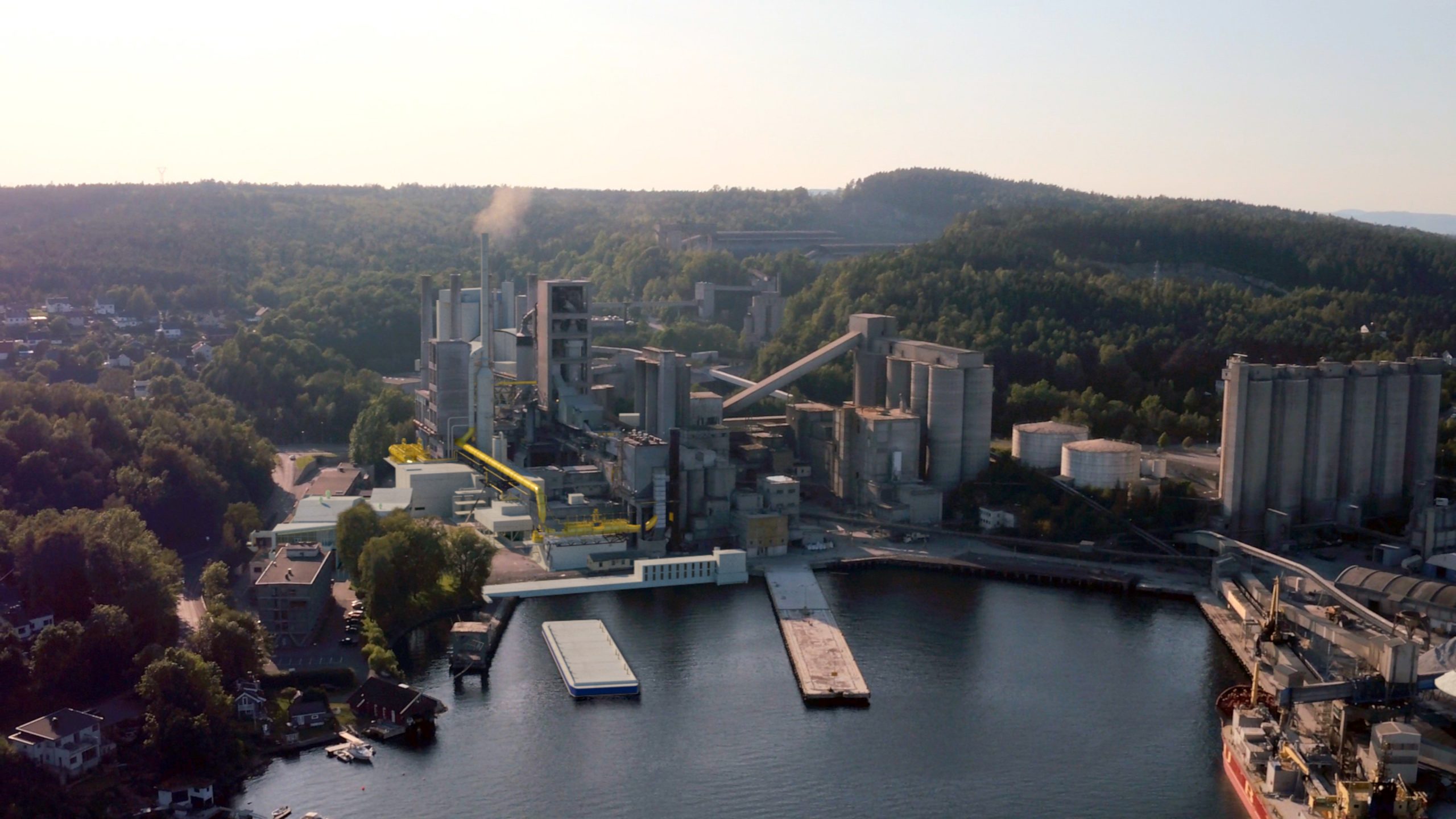
Image credited: Norcem Brevik Med CCS1
Cement is one of the most important commodities in the world. Norcem Brevik, owned by Heidelberg Cement, is the leading Norwegian cement supplier, aiming to become carbon neutral and reach national climate goals.
The Brevik Carbon Capture and Storage (CCS) project reduce CO2 emissions by 400,000 tonnes a year, paving the way for a net-zero carbon footprint for the cement lifecycle. Heat Management joins forces with Aker Carbon Capture by supplying powerful infrasound cleaning technology to keep the waste heat recovery boilers clean, thus maintaining a high heat transfer rate to maximize the boiler availability, efficiency, and lifetime.
Cement is the second most used commodity in the world after water, and the demand is increasing due to increased urbanization and population growth. Limestone is the key to make cement, breaking down limestone releases a significant amount of CO2, and there is currently no green option to match the characteristics of limestone. The Norwegian cement giant has taken innovative measures to tackle the problem from another angle, Carbon Capture and Storage. The Brevik CCS project is based on years of studies and testing, proving that CO2 capture is achievable.
The way it works is that flue gas is harnessed from the factory Chimney at Norcem Brevik. The flue gas is then cooled down by 30°C from 100-165°C in a direct contact cooler. The flue gas runs through an absorber, where the CO2 reacts with amine liquid, becoming an amine solution. Then the solution runs through a desorber, heating the liquid from 30°C to 120°C, separating the CO2, which can then be compressed and dried. This is an energy-intensive process that Norcem solves by utilizing waste heat from the cement factory. When the CO2 is returned to its liquid state, it is shipped by boat to a transit storage facility in Kollsnes. The result of the project is to avoid emitting 55 tons of CO2 per hour and 400 000 tons annually, which is equal to the emissions from about 200 000 cars per year.
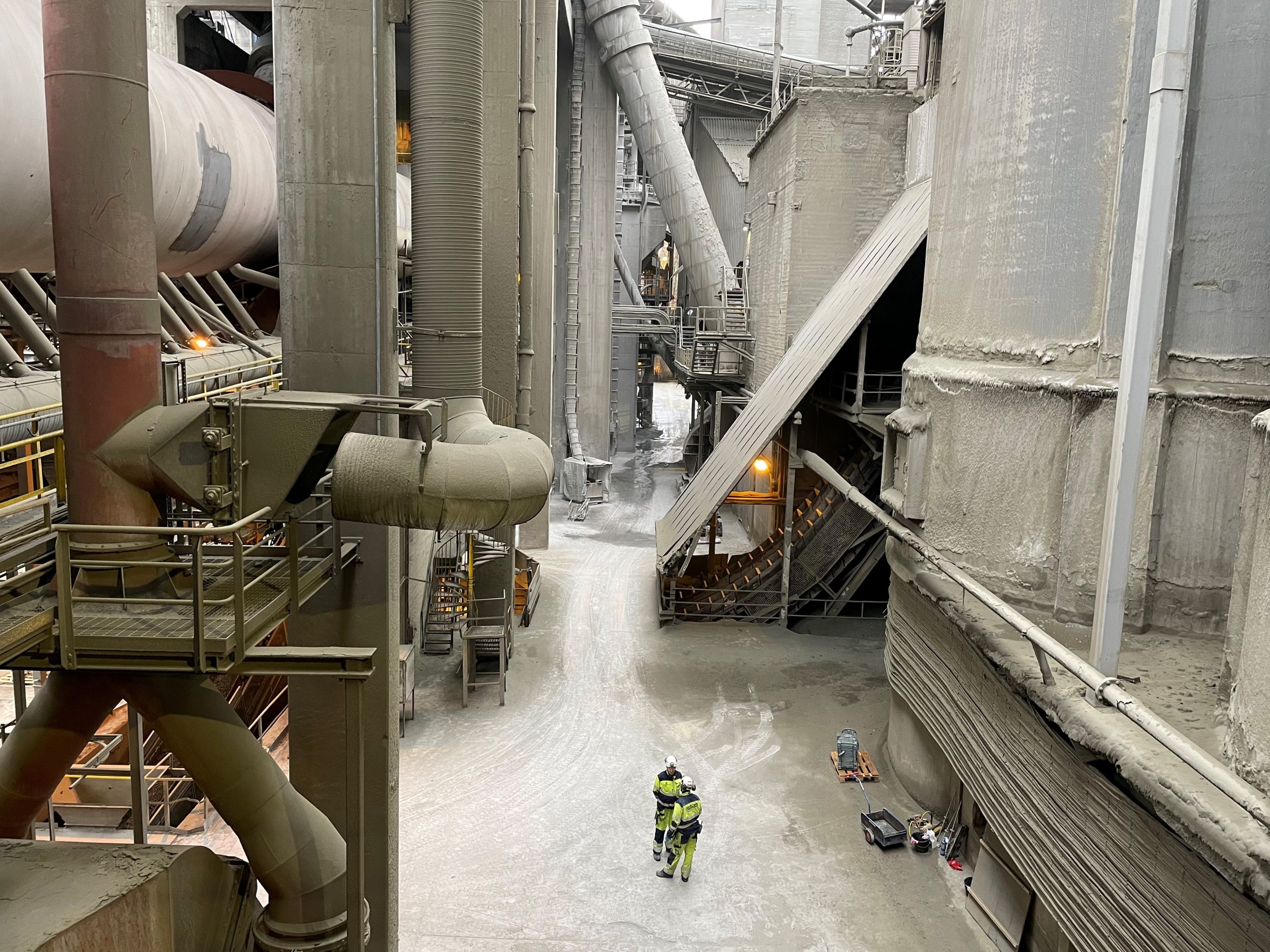
Image credited: Norcem Advansia
Cutting down on emissions and climate impact is a core value shared between Heidelberg Cement and Heat Management. Dirty boilers are a bottleneck for many companies. The cause of soot build-ups in boilers results in production losses, lower efficiency, unplanned stops for manual cleaning, among many other harmful effects. These issues cause unnecessarily high costs and environmental impact.
The Norcem project is a high dust application that often requires automatic, preventive, and dry online cleaning of all the heating surfaces. The unique Infrasound Cleaning system from Heat Management fit all the requirements and was successfully tested in a pilot plant before implementation in the full-scale plant. Heat Management ensures that the waste heat boilers run reliably and efficiently throughout the whole production year.
The sootcleaning system’s ability to help customers become more sustainable and save money simultaneously is what makes the system an incredible investment. More companies are encouraged to hop on the sustainability train, as sustainability is the new normal.